Нюансы применения ФБС блоков
Начнем с того, что существуют определенные запреты на использование бетонных фундаментных блоков. Под них нужна прочная основа, к примеру, скальная, на крайний случай, песчаная. Правда, современные технологии позволяют устанавливать ФБС даже на подвижные грунты. Просто придется вложить немало средств, чтобы подготовить грунт.
Обычно для этого формируют монолитную армированную бетонную площадку в виде плитного фундамента. А уже на него сооружают блоки с обвязкой по второму ряду армирующим поясом. По сути, получается тройной расход – плита+блоки+ленточный армированный фундамент. Добавьте сюда песчаную подушку под всю плиту, расход увеличивается.
Есть более дешевая технология. На основе ее получается прерывистый фундамент. Это когда блоки устанавливаются с промежутком, который в дальнейшем засыпается грунтом. Последний обязательно утрамбовывается. Но и тут есть свои запреты:
- расстояние между блоками – не больше 70 см;
- основа под них должна быть очень прочной с высокой несущей способностью.
Другой вариант, который используется на слабых грунтах, монтаж ФБС блоков с подпятником. Последний – это разновидность фундаментной подушки, изготовленной по технологии железобетонного изделия. Она имеет большие размеры, увеличивая таким способом площадь опоры. А соответственно, снижая давление на слабый грунт. На фото ниже такие подушки-подпятники показаны.
Подпятники для ФБС блоковИсточник st12.stpulscen.ru
При любой описанной технологии специалисты советуют приобретать железобетонные изделия с максимальной длиной. Чем меньше в сборном фундаменте стыков и швов, тем он надежнее.
Видео описание
В видео показана технология монтажа ленточного фундамента из ФБС блоков:
Плюсы и минусы ФБС блоков
В чем преимущества сборного блочного фундамента от монолитного:
- нет необходимости приобретать опалубку и арматуру для каркаса;
- после заливки монолита, необходимо время на его застывание и набора марочной прочности, на что уходит обычно 28 дней;
- сборный фундамент нагружать можно сразу после его монтажа;
- зная размеры ФБС, можно легко подсчитать требуемое количество материала;
- разнообразие размеров и характеристик, можно сэкономить, грамотно выбрав их;
- долгий срок эксплуатации – более 100 лет;
- высокая прочность материала, в процессе эксплуатации такие фундаменты не деформируются.
Что касается недостатков, то он один – большой вес изделия. Поэтому для сборки фундаментной конструкции приходится привлекать тяжелую технику в виде погрузчика или подъемного крана. К сожалению, их услуги недешевы, что увеличивает себестоимость строительного процесса.
Для монтажа ФБС блоков используется специальная техникаИсточник i.simpalsmedia.com
Коротко о главном
ФБС – это железобетонные изделия, используемые для формирования сборного фундамента.
ГОСТом предусмотрены различные размеры блоков, вес, характеристики и допуски.
Их используют для закладки фундаментов на прочных грунтах. Если грунты слабые или подвижные, то под фундамент заливается железобетонная плита. Сборный фундамент обязательно обвязывается армирующим поясом из бетона.
Время сооружения фундамента из ФБС – минимальный. Высокая прочность и долгосрочная эксплуатация привлекают потребителей. Минус один – большая масса, поэтому монтаж проводят с помощью специальной техники.
Фундамент из ФБС блоков, технология
Что такое фундамент из ФБС? Технологическая схема производства работ по строительству зданий из блоков предусматривает ряд последовательных мероприятий. Сначала выкапывается котлован, представляющий собой траншею. Для того чтобы исключить неудобства во время обустройства фундамента, следует знать размеры стройматериала, а также выкопать широкую траншею. Дно котлована очищается до породы, при этом неровности сглаживаются таким образом, чтобы основание стало ровным. Далее осуществляется засыпка основания песком.
Подготовительные работа по возведению фундамента
Для обустройства песчаного основания берется деревянный брус 50-100 мм по высоте. Насыпь осуществляется шире фундамента на 200 миллиметров. Для проверки ровности поверхности используется деревянный брус, заготовленный заранее. После установки бруса внутренняя часть рамки засыпается смоченным песком, либо проливается водой после засыпки и уплотняется. Начальный ряд укладывается шире основной части, что необходимо выполнять в целях увеличения площади основания. Для этого допускается применение фундаментных плит ФП. Также в качестве альтернативы возможно использование заливки основания монолитным ленточным фундаментом. Промежуток между плитами достигает 700 миллиметров. Первый ряд блоков укладывается так, чтобы вертикальные швы располагались над подушками.
Укладка фундаментных блоков
Для начала укладки фундамента из блоков ФБС необходимо определится с методом монтажа. Неправильно проведенная работа приведет к некачественному результату! Руководствуясь чертежом, специалист производит установку кольев, после чего по ним натягивается нитка. В целях упрощения укладки, прежде всего блоки, расставляются по пересечениям и в углах. Далее квалифицированный строитель заполняет вертикальные швы раствором, после чего следует утрамбовка землей.
Если все этапы осуществляются правильно, соответственно строгим требованиям технологии, между блоками возникнет пространство, которое в дальнейшем надо залить бетоном и выровнять. Выравнивание производится до получения между блоками монолитной вставки. Слой раствора должен быть не менее 15 миллиметров толщиной (между верхним и нижним рядами). Если говорить о вертикальных швах, то они должны перевязываться слоем бетона определенной марки. В целях усиления перевязки между рядами применяется арматура. Выполняя кладку бетонных блоков необходимо сделать отверстия, которые будут служить для отведения канализационных стоков и подвода воды.
Пошаговая инструкция по монтажу
Важнейшим этапом строительства фундамента из ФБС является грамотное проектирование.
Такую работу следует поручать профессиональным строителям, экономия на услугах специалистов может привести к серьезным последствиям, вплоть до преждевременного перехода здания в аварийное состояние.
На подготовительном этапе выполняется:
- разработка чертежей;
- проводятся необходимые расчеты;
- составляется четкий план работ.
Непосредственно перед началом строительства необходимо:
- подготовить стройплощадку,
- убрать мусор и лишнюю растительность,
- обеспечить беспрепятственный доступ для заезда спецтехники на территорию.
Земляные работы
Блоки могут укладываться в траншеи или котлован (если в здании планируется обустроить подвал). Ширина траншей высчитывается не по размерам ФБС, а по основаниям монолитных подушек, поскольку они являются более широкими.
Перед началом земельных работ необходимо выполнить разметку:
- определить углы здания,
- обозначить их маяками,
- между ними протянуть прочный шнур.
Глубина траншей и котлованов может составлять 1000-1400 мм. Это зависит от количества рядов блоков ФБС, уровня промерзания грунта и других факторов, учитываемых при разработке проекта.
Устройство подушки
Чтобы исключить вероятность проседания фундамента и стен здания, на дне траншей и котлованов обустраивают подушки.
Для их создания используют песок (нижний слой толщиной до 200 мм) и щебень (засыпается поверх песка таким же слоем).
Материалы необходимо засыпать поэтапно, через каждые 10 см нужно утрамбовывать пласты, чтобы придать им необходимую плотность.
Трамбование целесообразно выполнять при помощи специальной виброплиты. Чтобы добиться более качественного уплотнения и ускорить процесс, следует обильно увлажнять материал.
Обустройство подошвы
Подошву, на которой в дальнейшем будут установлены блоки ФБС, можно изготовить двумя способами:
- из готовых блоков ФЛ;
- путем создания монолитной конструкции.
Первый способ более простой и менее затратный. Блоки ФЛ чаще используют на плотных малоподвижных грунтах. Изделия размещают поверх подушки, после чего заполняют бетоном швы между ними.
Поверх гравийно-песчаной подушки создают опалубку из обрезных досок, внутри нее размещают арматурных каркас в два уровня (верхний и нижний). Далее опалубку заполняют бетонной смесью, марка которой выбирается индивидуально для каждого проекта.
Когда бетон наберет заданную прочность (1-2 недели), можно приступать непосредственно к монтажу ФБС.
Укладка блоков
Для установки ФБС используется автокран, поскольку ручная кладка невозможна из-за большого веса изделий (1-2 тонны, в зависимости от размеров).
Блоки укладываются на цементный раствор, которым также заполняют и вертикальные швы между элементами.
Монтаж ФБС начинают с угловых зон. По первым установленным блокам протягивают шнур, который используют для более ровной установки следующих блоков.
Создание армопояса
Когда все блоки ФБС установлены по периметру фундамента, необходимо подготовить армирующий пояс. Этот конструктивный элемент служит для упрочнения основания и повышения его прочностных характеристик.
Первый этап – создание опалубки. Для этого поверх блоков ФБС устанавливаются обрезные доски, которые необходимо надежно закрепить между собой.
В опалубке устанавливается арматурный каркас из стальных прутьев толщиной не менее 12 мм. Количество арматуры и размеры ячеек, образуемых продольными и поперечными металлическими стержнями, определяется при разработке проекта. В большинстве случаев устанавливается от 2 до 4 продольных прутьев.
Завершающий этап – заливка бетонной смеси в опалубку. После ее затвердевания деревянный каркас демонтируют.
Обустройство гидроизоляции
Железобетонные блоки ФБС чувствительны к воздействию грунтовых и атмосферных вод, поэтому создание гидроизоляционного слоя является обязательным этапом строительства фундамента.
Допускается использование любых подходящих материалов – как рулонных, так и жидких.
Во многих проектах применяются битумные мастики, которые легко наносятся на боковые поверхности блоков и обеспечивают надежную защиту от влаги.
Технические характеристики
Полнотелые элементы имеют отличные технические характеристики для возведения стен и цокольных этажей домов.
В соответствии с нормативным документом ГОСТ можно отметить следующие размеры изделия:
- Длина 400 мм;
- Ширина 200 мм;
- Высота 200 мм.
Вес полнотелого материала может достигать 31 кг. Он отличается высокой плотностью и прочностью.
Следует отметить такие характеристики:
- Прочность изделия зависит от веса и может составлять 25-75 кг/см2;
- Плотность может быть 2250 кг/м3. Пустотелые элементы имеют более низкую плотность;
- Морозостойкость материала составляет примерно 50 циклов;
- Срок службы изделия превышает 100 лет;
- Теплопроводность находится в пределах 0,51-1,14 ВТ/м*С.
Разновидности изделий
Блочная продукция из железобетона делится на различные виды, которые отличаются следующими моментами:
- конструктивными особенностями. В зависимости от исполнения могут присутствовать внутренние полости, в которые устанавливается арматурный каркас;
- габаритами и массой. Наружные размеры ФБС блоки имеют различные. Длина продукции составляет от 88 см до 238 см при массе 310–1300 кг;
Виды изделий ФБС
- применяемой при изготовлении маркой бетона. Используются бетонные смеси, маркируемые М100 (В7,5), М150 (В12,5), М200 (В15);
- уровнем шероховатости наружной поверхности. Внешняя поверхность может быть гладкой или шероховатой для лучшего сцепления со штукатуркой.
Технология производства фундаментных блоков
Технология изготовления фундаментных блоков ФБС на формах, как разборных, так и кассетных, включает в себя следующие основные этапы:
1. Приготовление жесткой бетонной смеси из цемента, заполнителя и воды.
Раствор лучше всего готовить в бетономешалке принудительного типа (т.е. со смешивающими лопастями). Из предлагаемого нами ассортимента это модели смесители Вибромастер РП-200 и Вибромастер СБ-80. Бетономешалки гравитационного типа («груши») использовать можно, но получить при этом качественное смешивание не получится.
Смешивать также можно и вручную, лопатой в любой емкости. При этом для приготовления жесткой смеси потребуется значительные физические усилия. Крайне мала будет и производительность такого перемешивания.
2. Цикл вибропрессования, состоящий из следующих этапов:
- Загрузка раствора в форму (производится вручную)
- Уплотнение в форме лучше всего производить с помощью глубинного вибратора. Уплотнение в форме под действием вибратора занимает обычно несколько минут. Это время и качество уплотнения зависит в основном от вибратора.
- Выемка блоков ФБС из формы происходит не ранее, чем через сутки (без использования ускорителя твердения ХК). При условии использования в производстве ускорителя твердения ХК – выемка блоков ФБС, как правило, производится один раз за 8-часовую рабочую смену.
3. Необходимый набор прочности.
Набор первоначальной прочности (достаточный для складирования) происходит при естественной температуре не менее 24 часов (без применения специальных добавок — ускорителей твердения – ХК, релаксола и других). Это время в данном случае зависит только от свойств цемента и температуры окружающего воздуха.
При использовании указанных ускорителей твердения это время может быть уменьшено до 5-8 часов (в зависимости от дозировки ускорителя). Очень желательно в первые дни набора прочности предохранять блоки ФБС от пересыхания. Для этого достаточно накрывать их полиэтиленовой пленкой. Также можно время от времени поливать блоки ФБС водой.
Набор отпускной прочности (согласно ГОСТ — не менее 50% от расчетной окончательной) происходит при положительной температуре примерно в течение недели. После этого периода блоки ФБС уже можно продавать потребителю и использовать в строительстве.
Набор 100%-ой прочности протекает в течение 28 суток при положительной температуре.
Вы также можете посмотреть следующие разделы
- Исходные компоненты
- Сертификация
- О нашей марке «Вибромастер»
- Полезные статьи
- ГОСТы
Лучшие керамзитовые строительные блоки
Элементы такого типа используют для создания разнообразных перегородок, кладки стен в малоэтажных зданиях, формирования фундаментов деревянных срубов. При производстве используют тяжелые, легкие или мелкозернистые бетоны. По типу конструкции их относят в основном к пустотелым, что предусматривает наличие воздушных карманов. Материал получается легким, но менее прочным. Он лучше переносит изгибающие нагрузки, а стены не требуют армирования, что позволяет ускорить стройку. При этом керамзитобетон сильно поглощает воду, поэтому нуждается в наружной отделке. Его не используют при строительстве бани, перегородок в санузле. По своим показателям он сильно уступает другим бетонным блокам. Из 5 заявленных номинантов лучшими параметрами обладают 2 типа элементов.
ФБС
Блок используют для цоколей и стен подвалов в зданиях всех типов. Полнотелая конструкция обеспечивает повышенную прочность, которая позволяет выдерживать нагрузку до 32 кг/см2. Содержание радионуклидов в составе не превышает допустимую норму. Гладкая конструкция и малый вес значительно упрощают кладку, последующую отделку.
Достоинства
- Высокий уровень несущей способности, морозостойкости, огнеупорности;
- Низкая цена;
- Хорошая звуко-, теплоизоляция;
- Компактные размеры;
- Устойчив к агрессивным химическим веществам.
Недостатки
- Тяжелый;
- Хорошо впитывает воду, что способствует разрушению структуры.
Не все покупатели довольны качеством товара. Они подтверждают его высокую прочность, морозостойкость, но отмечают некоторое несоответствие размеров.
Коломна
Номинант изготовлен из керамзита, воды и цемента, поэтому его считают экологически чистым товаром. Компактные размеры позволяют увеличить полезную площадь помещения. По классу прочности он не уступает предыдущему номинанту, но степень морозостойкости рассчитана лишь на 50 циклов. Последний параметр менее важен, так как блоки используют в основном для внутренних перегородок здания.
Достоинства
- Низкая цена;
- Малый вес;
- Высокая прочность;
- Устойчив к воздействию мороза и огня.
Недостатки
Высокая степень водопоглощения.
Внешний вид элементов неэстетичный, поэтому облагородить интерьер помогает внешняя отделка. Также она защитит материал от излишнего поглощения влаги при возведении конструкции вблизи ванной комнаты. К плюсам относят прочность, долговечность, безопасность для здоровья.
Достоинства и недостатки
Неоспоримые преимущества блоков ФБС можно выразить так:
- Все изделия изготавливаются согласно нормам ГОСТ, соответственно вне зависимости от производителя имеют стандартные типоразмеры.
- Производство ФБС подразумевает строгий контроль технологического процесса, что обеспечивает высокую прочность и надёжность продукции.
- Удобство монтажа и высокая скорость строительства: уложить фундамент и возвести стены из блоков можно буквально за 2-3 дня.
- Простота. Монтаж конструкций из блоков не требует специальных навыков и знаний в области строительства.
- Широкий размерный ряд. Эта особенность позволяет возводить сооружения с любым уровнем геометрической сложности.
- Блоки не требовательны к условиям эксплуатации, поэтому отлично себя чувствуют в любой среде. При изготовлении применяют специальные добавки, которые позволяют использовать блоки на влажных грунтах.
К недостаткам можно отнести такие моменты:
- При монтаже обязательно приходится использовать строительную технику, что увеличивает стоимость работ.
- Приходится укладывать между стыками слой гидроизоляции.
- Бетон не держит тепло, поэтому потребуется дополнительное утепление.
- Монолитный фундамент намного прочнее составных конструкций.
Кроме этого, блоки ФБС не рекомендуется использовать на заболоченных грунтах.
Технические особенности
Размеры блоков
Изготовитель обязан обеспечить блоки ФБС размерами, соответствующими ГОСТу с необходимыми свойствами и геометрическими параметрами. Любое несоответствие может негативно отразиться на постройке, привести к порче здания.
Блоки ФБС передают форму параллелепипеда, изготовленного из различных видов бетона: силикатного, керамзитового и бетонного. Плотность его составляет 1800 кг/м3, пустот не имеет, но содержит технологическую формовку для армирования по вертикали кладки раствором. Размерами 200х200х400 и классом прочности не менее чем В 7,5.
Изготавливаются и уплотняются конструкции на вибростолах, создается необходимый размер блоков ФБС, гладкость поверхности, а также плотность специальными опоками. Неправильная геометрия изделий не позволит выполнить ровную кладку, а швы по толщине могут превышать норму, которая соответствует 2 – 5 мм.
Таблица размеров на блоки, которая регламентируется ГОСТом.
Фундамент из блоков ФБС
Обычно после букв, которые указывают на тип изделия, присутствует набор цифр. Они указывают на габариты и, как правило, измеряются в дециметрах.
Первое число указывает, какая длина устройства, вторая – ширина, а третье значение – это высота.
Габаритные размеры фундаментных блоков указываются с округлением к большему значению. Вес даже самых незначительных изделий доходит до 260 кг.
Как выбрать?
Перед тем как приобрести фундаментные блоки, нужно ознакомиться с их техническими характеристиками и узнать о производителях, которые выпускают их в регионе.
Ориентироваться нужно на следующие факторы:
- климат региона;
- тип грунта;
- этажность и высота постройки;
- планируемая толщина стен и перекрытий;
- общий вес сооружения;
- площадь основания.
Для промышленного строительства используют крупногабаритные фундаментные блоки из бетона тяжелых марок.
Для возведения частных построек типа коттеджей или гаражей используются малогабаритные железобетонные блоки.
Для дачи, имеющей каркас из легких строительных материалов: дерева или пеноблоков, неуместно тратиться на основательный фундамент, в этом случае можно использовать легкие фундаментные блоки из силикатного или керамзитового бетона. Облегченные ФБС можно укладывать вручную без использования специальной техники. Здесь уместны будут блоки с параметрами 20 х 20 х 40 см.
Для беседки или подсобного помещения можно выбрать газобетон.
Кроме того, при выборе необходимо обратить внимание на производителя
- Лучше, если блоки будут заводского производства, поскольку в этом случае они проходят многоуровневый контроль качества и соответствуют ГОСТу.
- Зарекомендовавший себя производитель не только предоставит весь пакет документов, но и предложит гарантию или рассчитает расход материалов.
- Для строительства жилых или крупногабаритных сооружений лучше приобретать блоки с запасом прочности, например, армированные.
Если технология производства не нарушена, то ФБС прослужат долго (до 50 лет). Исключение составляют блоки с добавками доменного шлака. Эти изделия со временем разрушаются, а не крепнут, поскольку шлак с течением времени разлагается. Поэтому приобретать ФБС такого типа можно только для временных или технических построек.
Важной характеристикой при выборе является геометрическая форма ФБС. Идеальная геометрия позволит оптимизировать расход цементного раствора и затраты на отделку
А также она улучшит качество соединительных швов. Самые лучшие показатели в этом плане у керамоблоков и пенобетона.
Если рассматривать все характеристики в совокупности, то самыми выгодными по соотношению цена – качество являются керамзитобетонные изделия и пенобетон. При сравнительно невысокой стоимости они обладают высокими коэффициентами морозостойкости, отличными энергосберегающими свойствами, хорошей прочностью.
Фундаментные блоки
Фундаментные блоки сплошные (ФБС) – едва ли не лучшее решение при возведении как небольшого строения, так и многоэтажного дома. Фундаментные блоки обладают лучшими качествами, которые позволяют создать прочное и надёжное основание для жилого дома или производственного строения. Блоки изготавливают по специальной технологии, чтобы придать им требуемые качества. Благодаря этому они могут использоваться в достаточно жестких условиях без потери прочности и структурной целостности. Производятся они в соответствии с ГОСТом, что также даёт возможность заранее рассчитать конструкцию возводимого здания.
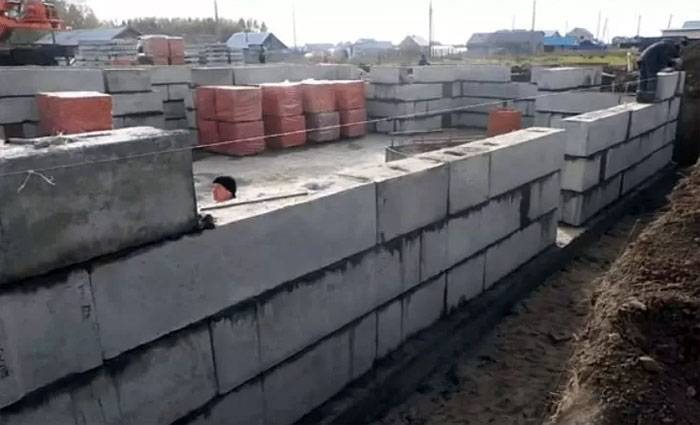
Область применения железобетонных блоков крайне широка. Их успешно используют как в масштабном строительстве промышленных комплексов или многоэтажных жилых зданий, так и при возведении одноэтажных частных домов. Исключительные характеристики получаемых конструкций сделали этот вид строительных материалов очень популярным. Они также нашли применение в качестве опорных элементов для технологических сооружений, к примеру, эстакад.